Ribbon Fiber Optic Cable and Splicing: Key Points and Considerations
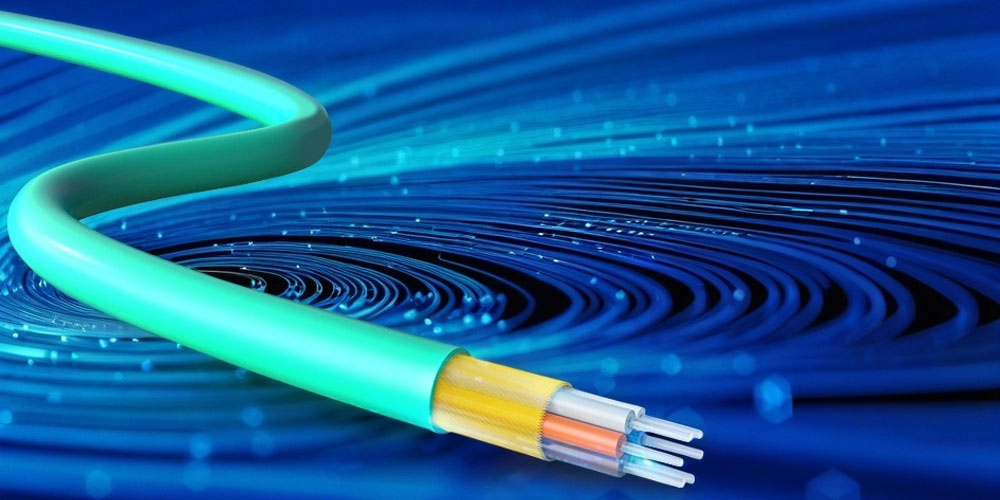
The technology of ribbon fiber optic cables is well-established in the telecommunications industry and is favored for its high fiber density and compact size. While traditional fiber optic cables contain individual fibers encased in a protective jacket, ribbon fiber cables organize fiber optic strands in a flat ribbon structure, creating freedom with space conservation and cable management. Of course, this ribbon structure also allows for faster and less expensive fiber optic ribbon splicing – especially advantageous when considering the mass fusion splicing technique, which connects multiple fibers at the same time.
The growth of ribbon fiber splicing is essential with increasing demands on network capacity, and it is becoming even more important in locations such as data centers, FTTH deployments, and in large-scale backbone networks, where an increase in capacity is in widespread use. This article will provide a brief discussion of ribbon fiber optic cables and ribbon fiber splicing, as well as the advantages of, challenges with, and best practices for ribbon fiber. With some background into the technology, the network planner/technician can make informed decisions to speed up the installation process, save on costs, and ensure fast, reliable data transmission.
Understanding Ribbon Fiber Optic Cable
Ribbon Fiber Optic Cable is a distinct type of fiber optic cable that features a series of optical fibers attached side-by-side in a flat, ribbon-type format. The cable is sometimes referred to as ribbon wire or ribbon cable fiber optic. All ribbon cables utilize fibers that are bonded together in groups, usually from (4 – 24) fibers = (12) fibers per ribbon. Normal examples of ribbon cables can be found with a (12) fiber system. The flat ribbon structure allows for the dense packaging of fibers, making it an ideal solution for applications where space is at a premium, such as within data centers or telecommunications rooms.
In most cases, fiber optic cables are designed in the traditional (loose tube) configuration – introducing fibers into small tubes but leaving them loose, in some cases. Ribbon Fiber cables offer a different design in which fiber will come loaded into a parallel matrix with each fiber in a precise place. This design precipitates the ability for fiber optic ribbon splicing (often referred to as Ribbon Fiber Splicing as well), through the mass fusion splicing technique, meaning that the operator can splice multiple fiber ribbons at once, greatly reducing install time, job time, and associated labor.
Because the ribbons are compact, the total wire that is being installed occupies less duct space and overall uses cable more effectively.
Innovations like Corning Flow Ribbon and RocketRibbon concepts have continued to improve these cable families. Corning Flow Ribbon fiber optic has introduced flexible ribbons with even smaller diameter fiber, so there is increased flexibility and reduced install times. Rocket Ribbon is even more astonishing as it pushes fiber counts to thousands all in one ribbon cable; this gives ultra high-density deployments without meaning the cable gets larger.
For example, Corning RocketRibbon extreme density cable has up to 3,456 fibers, which is the same outside diameter as the cable that holds (72) fibers, allowing the operator to install more capacity in the same duct, while reducing installation time by (30) percent. These larger fiber counts and efficient splicing, combined with usable designs, make ribbon cables a strong solution for the next generations in high-capacity networks.
Advantages of Ribbon Fiber Optic Cable
A significant advantage of ribbon fiber optic cable is its high efficiency in splicing, especially for splicing ribbon fibers utilizing mass fusion splicing methods. With mass fusion splicing, rather than splicing one fiber to another as done with a traditional fiber splice, a technician is able to splice 12 or more fibers in unison. The efficiency of mass splicing drastically makes splicing about six times faster than splicing a single fiber. This significantly reduces the man-hours to complete an installation in comparison to splicing individual fibers, especially during installation on larger projects.
Another benefit of ribbon cable is the overall higher fiber density. The flat configuration of ribbon cables allows for connecting more fibers in a smaller area; thus, using and optimizing the utilization of space in duct and equipment racks. Ribbon fiber cables are great for applications that require high capacity connectivity, for example, data centers, and also with backbone networks.
A case study from a major data center in Europe identified the use of flexible ribbon fiber cables improved cable management, reduced cable congestion, and improved the expansion of networks quicker with the use of flexible ribbon fibers.
Ribbon fiber optic cables also allow for simple bandwidth and network scalability as the increased number of fibers in a single cable allow for ease to expand the existing network without needing to add additional cables or conduits. These scalability efforts also support the growing demand for data usage and future use of deployment.
Lastly, the combined efficiency of mass fusion splicing, higher fiber counts, and cable organization/capacity make ribbon fiber cables a cost-effective solution to a large-scale deployment. Cost savings through the reduction of labor time and materials contribute to the overall project price, in a similar way that ribbon fiber optics can be a cost-efficient solution for the modern network. The Vancouver Fraser Port Authority’s Centerm Expansion Project was recently completed with over 100 km of fiber installed with a substantial reduction in labor hours due to both the use of ribbon fiber cable as well as mass fusion splicing.
Challenges and Considerations of Ribbon Fiber
Though ribbon fiber optic cable can offer many advantages, it has its own set of challenges that installers and network planners need to be aware of. The most significant difference in handling ribbon cables is that they have a limited bend radius and less flexibility over traditional “loose-tube” fiber optic cable. The flat, bonded structure of ribbon wire makes it much more rigid. As a result, it is much more difficult to route fiber optic cable in cramped spaces or in complex routing situations. If the bending radius is improper, it could introduce microbends or macrobends to the cable that degrades the signal or even damages the fiber.
Handling and installing ribbon fiber optic cables is something that you need to be careful about to avoid stressing the cable. The rigidity of ribbon fiber installations will require the person installing it to take care in planning their installation to avoid excessive tension and adhere to the minimum bend radius. This is especially true when routing cable that may come into contact with any kind of friction or movement of the cable in the environment or through small conduits.
Quality of the ribbon fiber splice is also critical. Because mass fusion splicing is done at once with multiple fibers and needs to be in alignment, there is a need for very specific technique and well-maintained equipment. If the splicing is not completed accurately, it will increase the insertion loss or its reflectance and begin to degrade the network performance. There will also be a need for the technician to be trained to perform fiber optic ribbon splices to make sure the splice is of good quality and will consistently have a lower loss splice.
The environmental concerns such as temperature concerns, moisture, or mechanical flex will all impact the fiber cables. Cable protection and environmental sealing will need to be considered to ensure fibers offer long-term reliability in any deployment scenario. Test facilities established at Ingalls Shipbuilding with field trials found that ribbon fiber splicing contains specific tools and training required, but in turn offers greater overall installation efficiency and stability under the conditions producing cable in an installation environment similar to a shipyard.
Ribbon Fiber Splicing Techniques
Splicing ribbon fiber optic cables involves some specialized skill sets and techniques to provide efficient and reliable connections. The two main types of splicing for ribbon fiber are fusion splicing (especially mass fusion splicing) and mechanical splicing (which is less prevalent with ribbon fiber applications).
When splicing ribbon fiber, mass fusion splicing is the choice method because it provides the ability to splice numerous fibers at the same time (typically 12 or more). The mass fusion splicing process involves aligning the ribbon of fiber in a precision splicer, and then an electric arc fuses the fibers together at the same time. Mass fusion splicing saves technician time and labor, and it is suited for high-density cable assembly, which is the only way to splice ribbon fiber in a way that reduces labor intensity.
Mechanical splicing may be a less skilled process, but it is not recommended for ribbon fiber cable, as it requires aligning and joining multiple fiber ends together in a physically joined manner using an alignment sleeve containing adhesive. Mechanical splicing produces higher insertion loss and is not as durable as fusion splicing.
The step-by-step process of fiber optic ribbon splicing begins with the ribbon fiber cable preparation. In this preparation process, the technician must strip off the ribbon protective coating carefully, so as not to damage the fibers during stripping, and thoroughly clean the fiber, then cleave the end of each fiber before trying to melt or fuse the fibers together. After stripping, cleaning, and cleaving, the fibers are aligned together and placed into a fusion splicer, which allows the technician to fuse all fibers together in one process cycle. This designed process allows for multiple high-quality spliced fibers spliced in one operation.
As far as splicing best practices, it is important to keep all splicing equipment and cleavers in excellent working order, and to ensure you have well-prepared clean optic fiber ends to align and fuse. Due to conditions being different, it is best practice to establish systematic splicing parameters based on fiber type and conditions to produce the lowest splice loss. This is also where cleanliness of the fibers during splicing can offset the worst splicing outcomes, as dust and debris will compromise the quality of a spliced fiber optic cable.
Some of the major tools used in the ribbon splicing process include thermal strippers, fiber cleavers, and ribbon fusion splicing tools that have been developed to handle multiple fibers. Using methods and techniques that involve the best equipment ensures low-loss splices that are reliable and efficient for modern high-capacity networks.
Innovations and Industry Examples
Corning Flow Ribbon technology is a major breakthrough in ribbon fiber optic cables. Their MiniXtend cable contains Corning’s Flow Ribbon, consisting of flexible, lightweight ribbons of smaller fiber diameter, which increases cable flexibility while maintaining fiber count and performance. These advancements increase deployment efficiency by facilitating easy routing through tight spaces and decreasing installation handling challenges often associated with traditional ribbon fiber cables. This ultimately eases network design, enhancing deployment speed, and optimizing space.
Flexible ribbon fiber cables are emerging as a leading choice in data centers as they can fit in cramped environments while preserving high fiber density. As a result, these cables are simplifying cable management and reducing congestion in racks and trays. There are already deployments that have illustrated flexible ribbon fiber cables can reduce installation and maintenance time, which corresponds to a reduction in operating costs and increases in network reliability. For example, HUBER+SUHNER’s OptiRibbon reports splicing time improvements of 60% or more, solving technician shortages and enabling faster network rollout.
Practical Tips for Working with Ribbon Fiber Cable
It is important to abide by helpful recommendations when working with ribbon fiber cable to ensure its proper function and durability. When handling and storing ribbon cable, keep the following considerations in mind. First, avoid excessive bending or twisting. Because ribbon fiber cables are flat, they’re more susceptible to damage or performance impairments due to repetitive bending. Second, cables must be stored clean and dry, and when coiled, for protective purposes, the loop must be loose to ensure stability.
During installation, it is critical to observe the minimum bend radius and avoid sharp bends or kinks that will degrade the fiber or cause a complete break. Additionally, using proper cable management tools will allow the technician to secure and route the cables with little to no strain on the fibers.
Well-trained personnel is one of the most important factors in manufactured ribbon splicing. Understanding the fiber optic ribbon splicing technique and splicing equipment will lead to high-quality, low-loss, and efficient splices. Continued development of skills and practice will lead to successful ribbon splicing.
Some of the most common issues encountered during fiber splicing are splice loss and fiber damage from contamination or incomplete splices. Routine cleaning of splicing equipment, as well as a thorough examination of each splice when finished, will maintain the reliability of the connections and performance of the network.
Summary
Fiber optic ribbon cables and splicing technology bring significant benefits when used in a high-density, efficient, and high-throughput network installation. The most critical requirements for the fiber optic ribbon cables include considerations for splicing that are efficient, handling challenges due to the stiffness of the cable material, and consideration of installation technology that will require specialized tools/training. The newest product, Corning Flow Ribbon, continues to improve the installation flexibility and performance of materials for ribbon fiber optic installations.
Looking ahead, the ribbon fiber optic cable market is expected to grow rapidly as the demand for bandwidth in networks increases, data centers continue their growth, and the 5G wireless network is deployed. As they map out the future of their networks, planners of network construction and installation need to prioritize proper handling of the cable materials, splicing techniques, and the resulting technology for ribbon fiber optic cables for the highest network reliability and scalability. Given their prioritization of handling procedures, expert splicing processes, and then use of technology for ribbon fiber, planners can take advantage of the benefits of fiber optic ribbon, which provides faster mass fusion splicing, better usable fiber density, and easier-to-sell upgrade capabilities for customers. Together these technologies will help those involved in building fiber optic infrastructure make better decisions about the future of wiring structures and network installations.